Solutions for today and tomorrow
Corrugated cardboard
warehouse design
The reasons to switch to vertical storage are irrefutable from a technical, energy-efficiency and management point of view.
This structure is the solution for increasing production and reducing costs and losses in corrugated cardboard manufacturing processes.
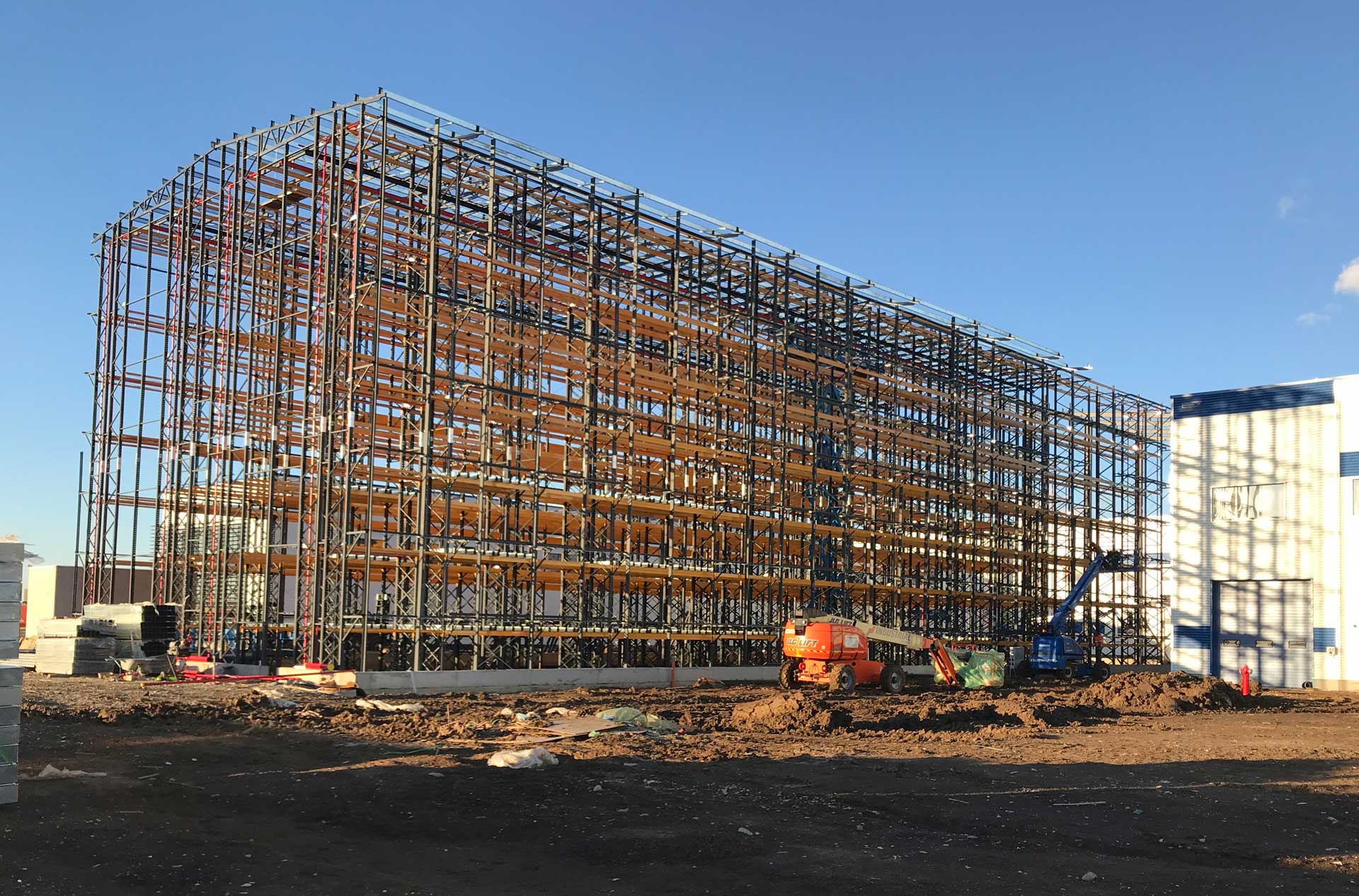
Flat conveying VS vertical storage comparison:
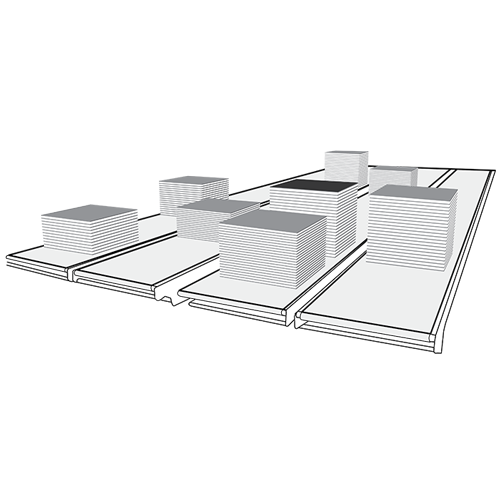
Flat conveying
- Limited to the FIFO system.
- 40% loss of operating area.
- Low stock control.
- Higher consumption per movement.
- High operating and maintenance costs.
- Losses as a result of manual intervention.
- Difficult compliance with RBC food health regulations.
- Losses as a result of lack of traceability.
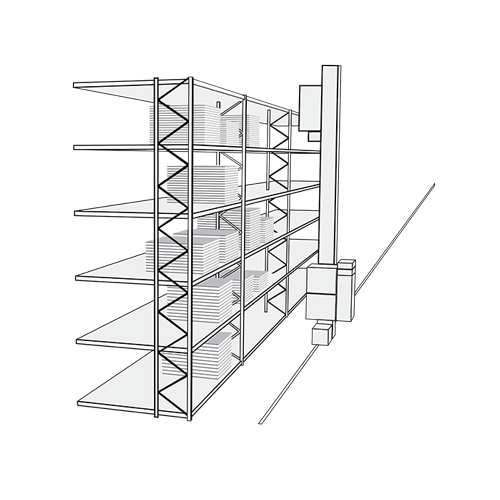
Vertical Storage
- Independent movement of stacks and elimination of the FIFO system.
- 3 or 4 times more storage capacity on the same surface.
- Integral stock control in real time.
- 80% reduction in components.
- 80% reduction in installed power.
- Better stack conservation and drying.
- Worker-free enclosure with 100% safety.
- Full label-free traceability.
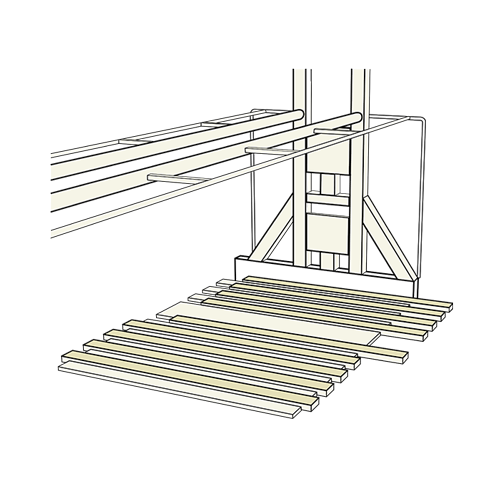
Warak advantages
- Rail dependent retrieval equipment for 5,5 meters board.
- Large-size cells with variable stack distribution.
- Intelligent drive forks for several orders at the same time.
- 3D digital simulation based on real production data.
- Remote stock and machinery control in real time.
- Full audit at any time.
Planning and control
4.0
Our IMOVE software offers key benefits for planning and stock control.
Imove handles at the same time several communication links with the different main actors of the factory: corrugator stacker exit, ERP system, converting machines and SGA from stacker cranes.
From ERP system receives the information of the planned production from corrugator and converting machines. Depending on the ERP system, we can receive the information of the production orders in file batches or constantly.
Requierements:
In the converting side, we must receive at least 4 planified orders for each converting machine.
With such information, we guarantee the delivery of corrugated stacks on time to any machine no matter the size of the orders.
From the corrugator and converting, we must receive all scheduled orders.
With such information, Imove is able alredy to prepare predictive reports on storage capacity and gives the information to operators to prevent future stoppages.
At corrugator exit, Imove combines the several stacks to generate the blocks which will enter the Rack or the stacks that will be delivered to converting machines or expedition area.
The main goal is to form the biggest possible block, combining stacks and orders with the target to optimize the cell space and the number of transport cycles. The blocks may vary depending on the real ocupation of the cells at an specific moment.
When board blocks cross the presses we implement a dimensional check and ID control. Checking theoretical weight and external dimensions. We avoid any missleading block going into the rack entrance.
Operator can mark and discard at ANY time and any station any block. Such block is sent to an emergency station to fix it or discard completely.
Any block with bad quality board can be marked as not good for converting. They can go inside the rack but when convertign request such blocks operator may decide which ones can be used partially or not and take them out of the rack.
Any block data sheet can be modified: -as an example-, the number of sheets for that block and the processes that will follow.
Depending on ERP scheduling system or handling equipment master control, Imove software will retrieve the blocks from the rack at a specific time. chooses which blocks must exit first from the rack. Organize the block downloads to guarantee the continuous feed of stacks to converting machines.
From imove we can monitor the whole factory, having acces to all data sheets of any block -in transit to rack or converting area- shown on the screen. Operator can delete or create a new block with different data on any station where he manually recomposed or modifed the block.
Imove stores the tracking of ALL blocks generated in the factory. There are many different events like: creation, address delivery, modification, etc…Such events are generated automatically and the tracking of the block throught different stations marked as decision points.
The tracking of any block can be checked individually or asking for a complete report.
Imove has different pre-configured filters to generate reports related to blocks. Rack occupation, input/output blocks to rack, Type of orders or any specific customer data as we use an SQL who synchronizes with rack SQL continuously.
Depending on the data from the ERP we can prepare a predictive report on the actual WIP situation at any time.
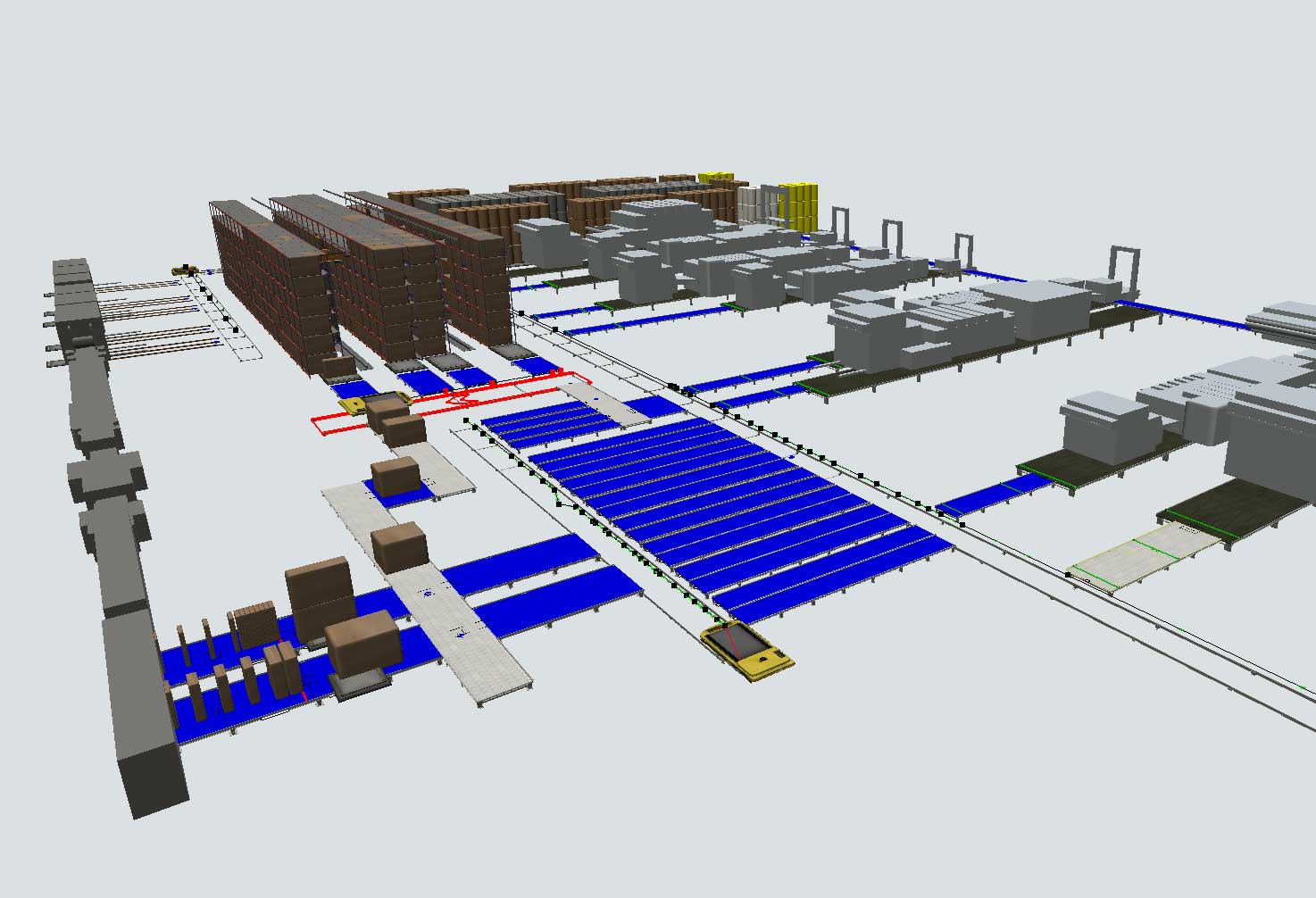
Customers talk
about us
Technical Director Romcarton - Rossmann Group
Guillaume Grandviennot talks to us one year after changing his flat storage structure to a vertical system.
If you would like to learn all the advantages a vertical installation can offer you, find out more about our viability study.